Victoria Player has an abundance of energy – when she’s not working as a forklift operator, she’s training for competitive triathlons, or doing hot yoga, snowboarding or hiking.
She does all that with the help of four prosthetic legs designed for different uses. Player, a 52-year-old from Belmont, Ont., describes them as an “everyday working leg, a blade runner, a “pretty” leg with an adjustable heel and a water leg for the beach.”
Recent years have seen extraordinary advances in the development of artificial limbs, powered by a combination of new resins and plastics from the petrochemical industry, computer technology and discoveries in artificial intelligence. Thanks to lightweight, flexible plastics derived from oil and gas, prosthetics now look and feel like the arms and legs they replace.
New materials like thermoplastic urethane, or TPU, are notable for their strength and elasticity. TPU, whose novel chemical structure allows it to be fine-tuned for density, can be made hard in some places and soft and fleshy in others — just like the human body. Meanwhile, advances in artificial intelligence have led to the development of prosthetic hands that can “sense” things like weigh and density, so the right amount of force can be applied to pick something up.
Player has definitely seen improvements over the seven years she’s been an amputee. “My everyday leg actually has movement and feels like an ankle joint,” she says.
Player was 18 when she was injured while working on a farm — a rack of tobacco fell on her left leg, badly damaging her ankle. For the next 27 years, she endured what seemed endless operations and hospital stays. A bout of osteomyelitis sparked the difficult decision to have her leg amputated below the knee. Thanks to a supportive family and state-of-the-art treatment, her quality of life quickly improved.
“It was the best decision I have ever made,” says Player. “With my amputation, I gained so much life back. I am able to positively impact others by sharing my story and showing others that an amputation does not have to be disabling. It can be extremely empowering and in my case [it gave] me greater ability to participate in all my favourite activities.”
Player got hooked on triathlons following her amputation, attending a para-triathlon camp in Florida. She raced internationally for one year and now competes in local races within her age group.
Sasha Boulton has also seen the benefits of improved prosthetics. A former elite athlete herself, Boulton, who is able-bodied, was forced to retire because of a back injury while still in her teens. She was initially frustrated, but an invitation to work with athletes with disabilities took her in a new direction. Today, she works with para-athletes — she participated in the Rio Games as a guide to a visually impaired triathlete and she’s also a coach. Those experiences, along with her biomedical engineering degree, have given her a unique perspective on how prosthetics support the goals of elite-level athletes.
“Prosthetics are definitely evolving,” says Boulton, who attended the University of Guelph. “They’re more flexible and waterproof, that’s one of the biggest differences. Things like reinforced polymers have really made a difference. Where before you would have biomaterials growing on an implant [like an artificial hip] which was a significant problem, now these things last much longer and they’re much more comfortable … It’s really revolutionized people’s lives.”
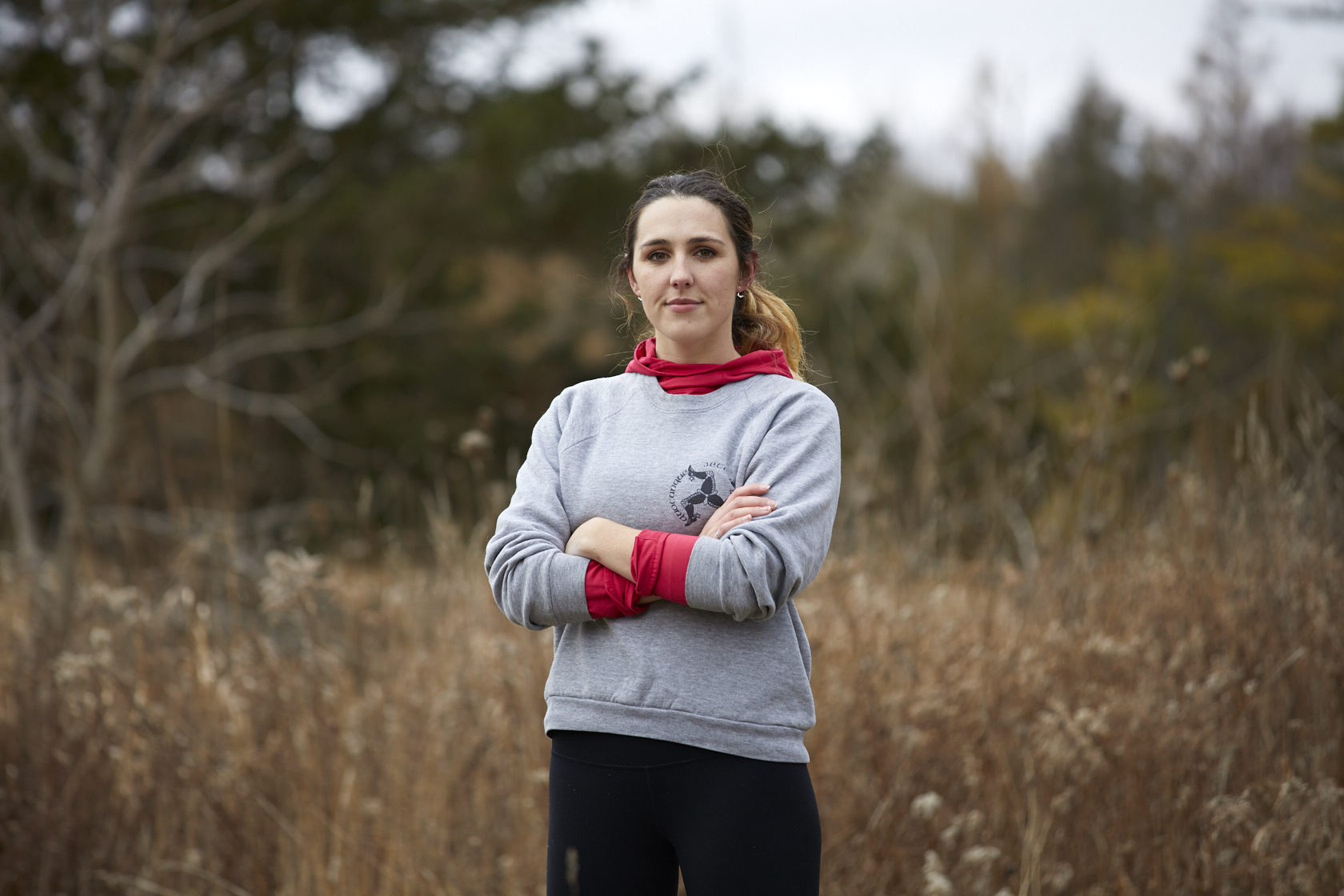
The potential of some of recent developments in prosthetics are head-spinning. Scientists at Duke University in the United States are working on technology that converts signals in the brain into electronic pulses that can be used to control a wheelchair or, potentially, an artificial limb. It’s early days yet. The science has been demonstrated with monkeys but it may be a while before regulators green-light human trials. But clearly it’s an opportunity.
The not-so-good news is that such futuristic prosthetics can come with a stratospheric price tag. The most advanced artificial limbs can cost $40,000 or more. Plus they take months to build and fit.
But change is coming on this front as well. Midia Shikh Hassan, a graduate of the University of Ottawa’s chemical engineering program, is making waves with a novel approach to making artificial limbs at a fraction of the cost of conventional ones.
Several years ago, she and a group of fellow students began thinking about ways to help war refugees. Together, they founded a company that uses 3D printing technology to manufacture prosthetics quickly and cheaply for clients virtually anywhere in the world. Dextra Innovations Inc. clients pay about $100 for an artificial arm, which takes about a week to make.
But Dextra is more than just a manufacturer. It’s a social enterprise that works with communities across the developing world to spread understanding of its technology so those communities can help themselves. Last year, Hassan travelled to the UK to receive the Young Leaders Award from Queen Elizabeth.
It all started when Hassan, who was born in Syria and emigrated to Canada at 17, became involved in helping to settle new immigrants from the Middle East in Ottawa. “I was helping them find jobs, start their own businesses,” she says.
While completing her engineering degree, she met up with a group of other students with similar scientific backgrounds. They also wanted to help refugees. So they decided to work together to come up with something, a product they could make, that would be beneficial to refugees and victims of war.
“We began thinking about healthcare applications and that’s when we came across prosthetics,” she says. 3D printing seemed an obvious route. Unlike conventional prosthesis manufacturing where design of prototypes and moulds can take months and cost a fortune, 3D printing, using a range of inexpensive plastics, can be done on a shoe-string budget.
Hassan speaks calmly, like the company CEO she is. But her tone changes when she talks about a recent client, a small boy in Morocco, who had lost both his hands. Because of the distance, they had to communicate by telephone and over the internet, and they couldn’t actually meet the boy. The first version of the prosthetics didn’t work so well and they could see from video taken of that first fitting that the boy was despondent.
“But we did not give up and we tried not just to fix but actually improve it,” Hassan says. “After two days he sent us a new video, and seeing the boy try out [the new arms]–I just remember my heart was overcome, not because I think what we’ve done is the best thing, but because we showed that little guy there are people who care.”